PCB Defluxing and Cleaning
Cleaning your PCBs – The Why and How
There are many reasons why a board could fail in the field. When you are manufacturing electronic circuits that are used in high-reliability applications, field failures resulting from dendritic growth, electrochemical migration, leakage current, and conformal coating, among others, are unacceptable risks.
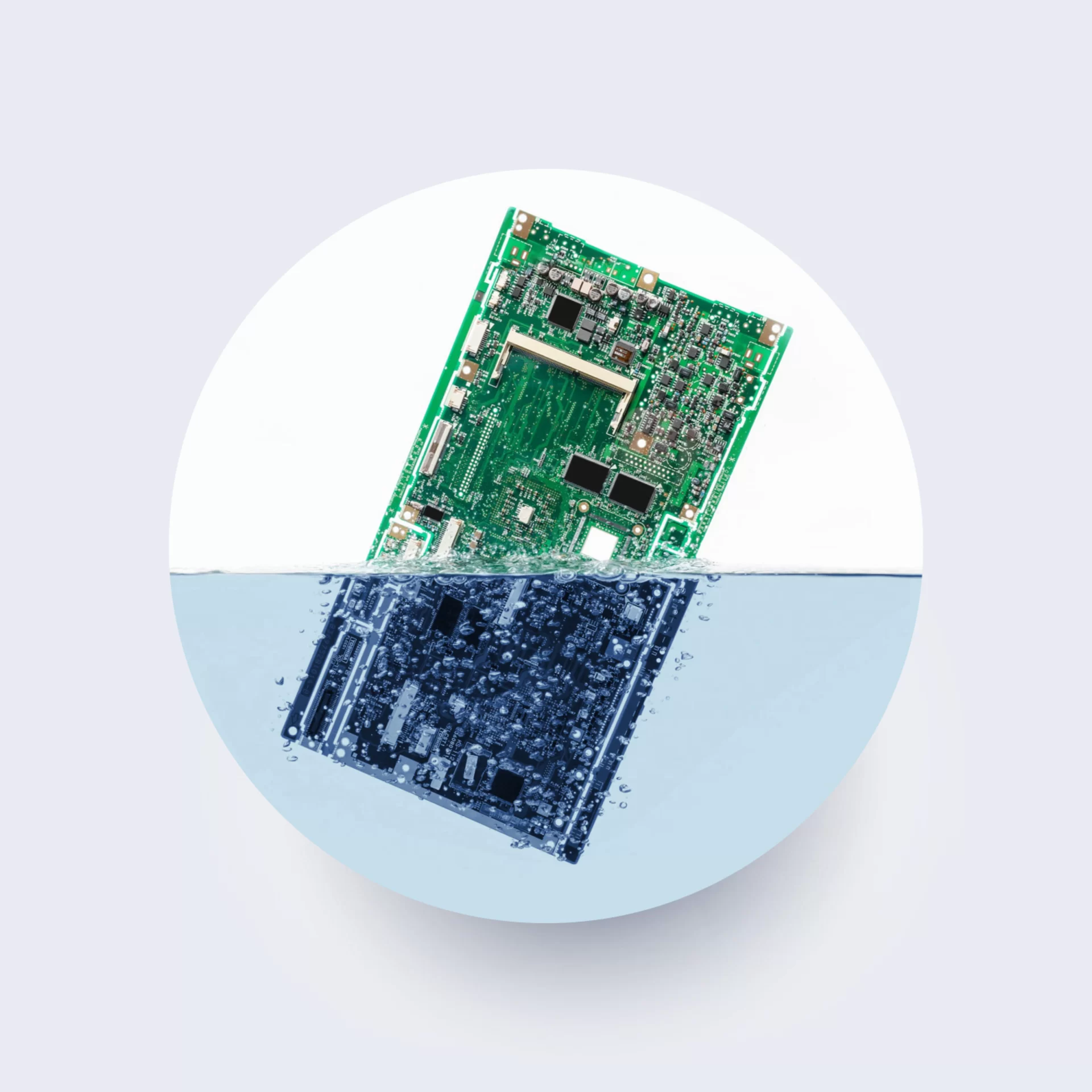
The Challenge of Cleaning Complexity
As technological applications become increasingly complex, so do the printed circuit boards that power them. Today, PCBs can do more while utilizing less space through the implementation of the following:
Industry Standard Equipment for Cleaning Your PCBs
Cleaning the circuit assemblies is a crucial part of any reliability engineering process — proactively mitigating risk by removing the contaminants that lead to field failures. There are industry standards established for cleaning PCBs and multiple options for cleaning depending on your production needs:
01
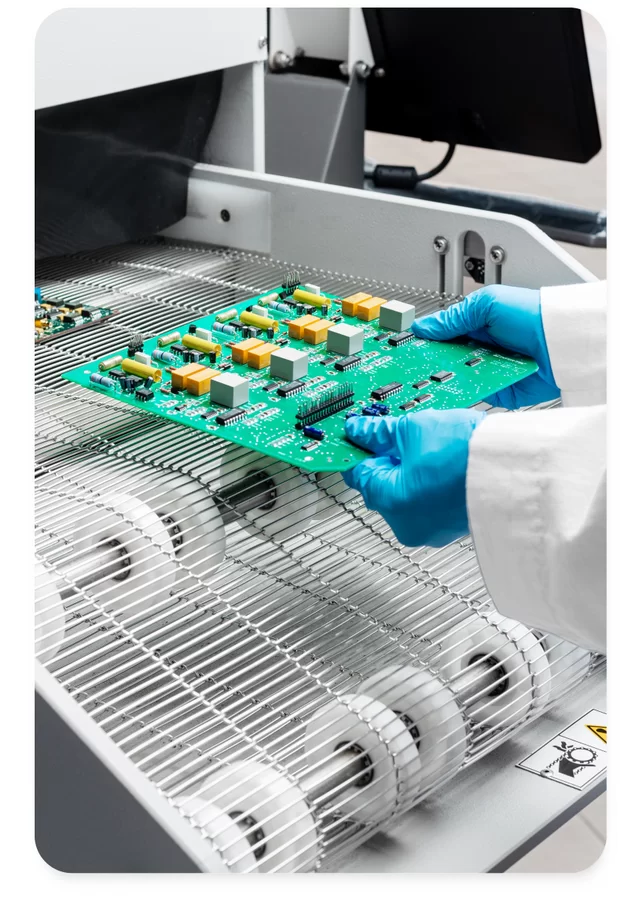
Inline Cleaning Equipment
High Volume Production
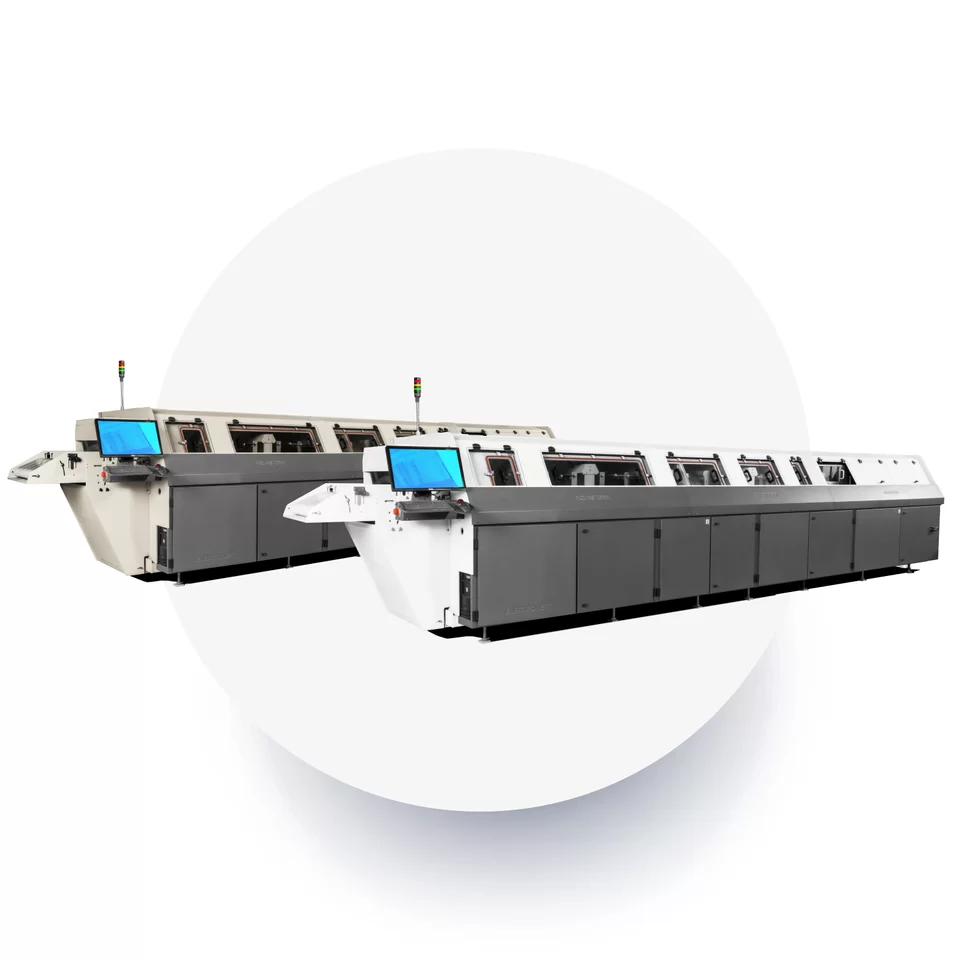
Spray-in-air inline cleaning machines are ideal when cleaning electronic assemblies with densely populated boards having low standoff components and when requiring high production throughputs.
The PCBs are placed on a Conveyor Belt and run through individual process steps, where cleaning, rinsing, and drying are performed in separate sections of the inline machine.
Batch Cleaning Equipment
Medium To High Volume Production
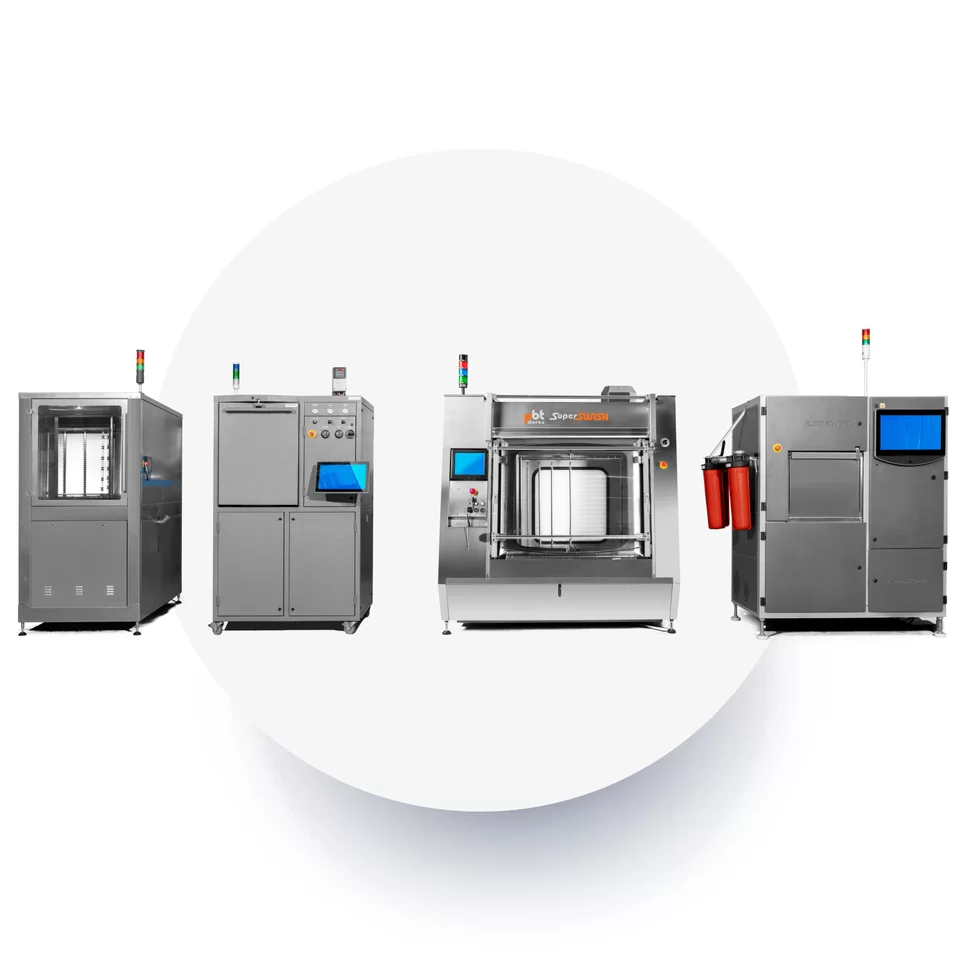
The spray-in-air batch system operates using technology very similar to the technology used in a dishwasher. All process steps are executed within the same process chamber. The cleaning medium is sprayed onto the electronic assemblies through nozzle fittings on rotating spray arms.
The cleaning effect is achieved primarily by the volume of cleaning medium passed over the substrates rather than the spray jet pressure like in inline processes.
02
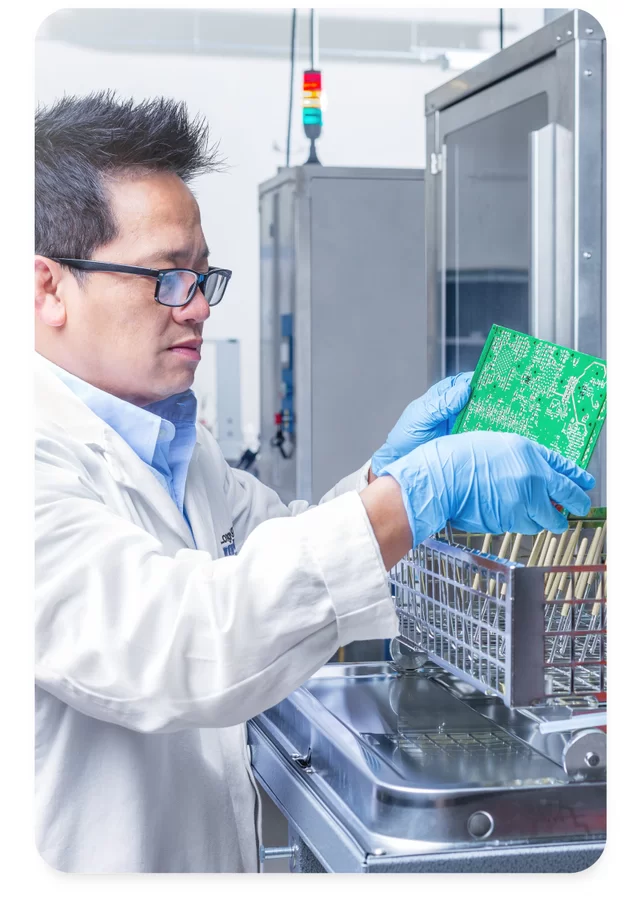
03
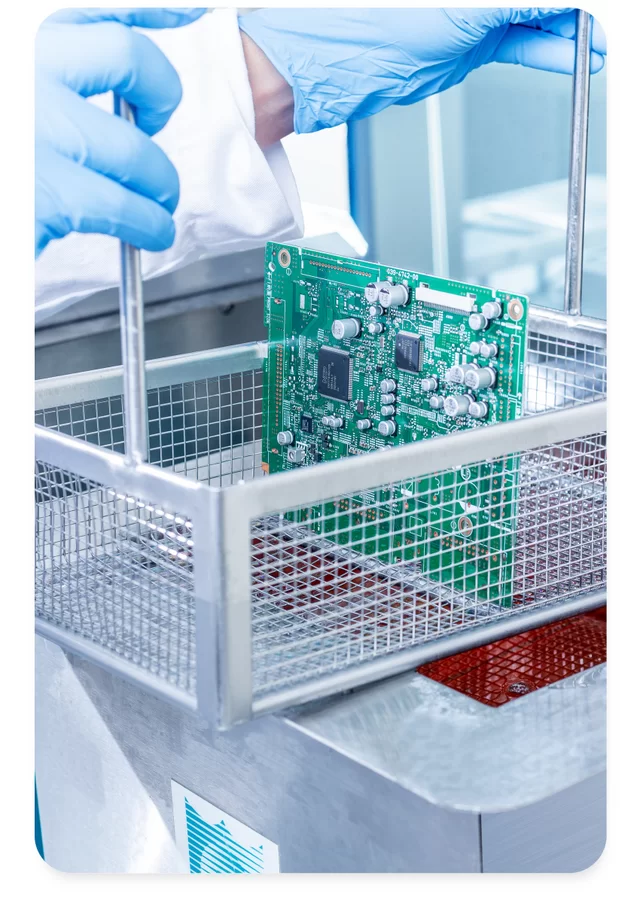
Ultrasonic Cleaning Equipment
Small to Medium Production
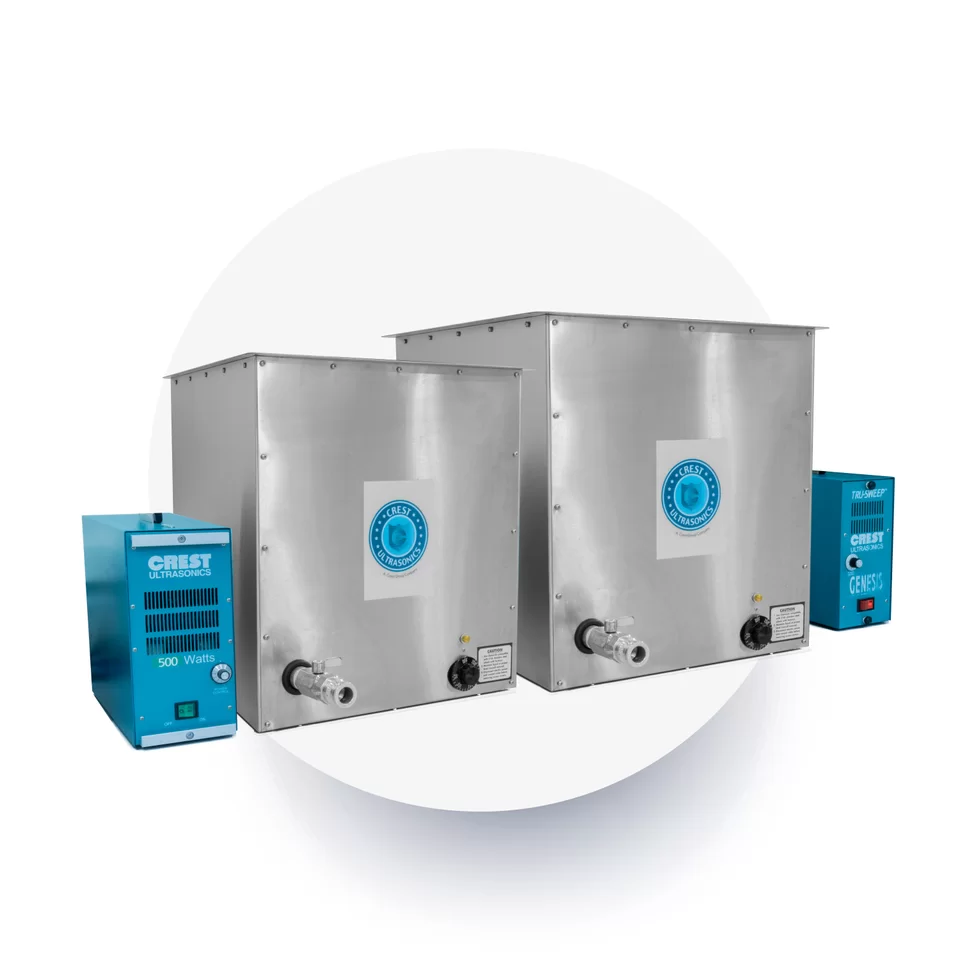
Ultrasonic systems submerse the PCB in a cleaning medium that is then agitated with soundwaves exceeding 20 kHz. Ultrasonic cleaning can be useful in cleaning under components and complex geometries since the sound waves are capable of reaching the populated circuit board from every angle.
Many industry cleaning machines have an automatic frequency adjustment for the modulation of the ultrasound (sweep) working frequency, which prevents “hot spots” and allows material-friendly cleaning.
Manual Cleaning
Small Production

Sometimes individual PCBs need to be cleaned with unique geometries and materials. In this case, nothing beats good, ol’ fashioned elbow grease. Manual cleaning requires no investment in equipment and is popular in applications where the throughput is low like building prototypes or performing electronic component rework/repair. If a facility is producing medium/high throughput, running several shifts and requires reliable and repeatable cleaning results, an automated cleaning process is recommended.
04
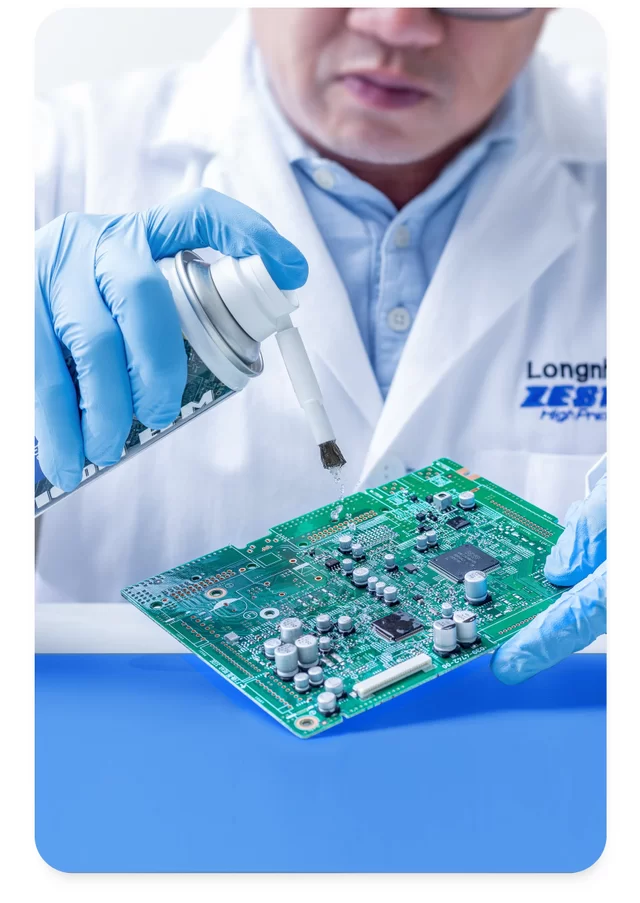